White fused aluminum oxide, also known as white fused alumina, stands as a premium material that belongs at the forefront of abrasive applications, refractories, and blasting processes. This synthetic mineral, created by fusing high-purity alumina in an electric arc furnace, showcases a set of characteristics that set it apart from other abrasive materials, earning its place as an invaluable asset in industrial and commercial applications alike.
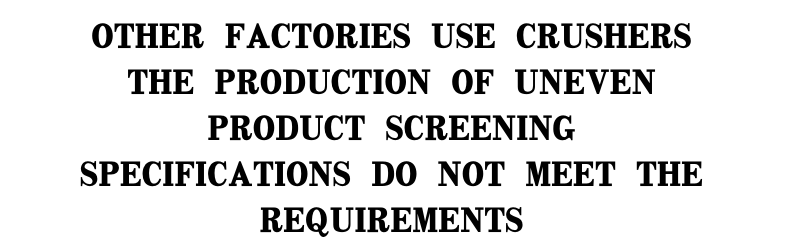
Manufacturers and industry experts often prefer white fused aluminum oxide for its remarkable hardness and strength, attributes that lend themselves well to the challenging environments of metal surface preparation and polishing. The material boasts a Mohs hardness rating of 9, just one notch below that of diamonds, indicating its impressive capability to efficiently abrade even the toughest surfaces. This feature positions it as an ideal choice for applications requiring durable and consistent performance, such as manufacturing conditions demanding precision and reliability.
Professional expertise dictates that the uniformity of white fused aluminum oxide significantly enhances process control. Its purity—typically above 99.5% Al2O3—ensures minimal contamination of the materials being worked on. This is particularly vital in highly regulated industries, such as aerospace or medical sectors, where the slightest impurity could lead to significant defects or failures. Processes that involve critical component finishing benefit from the consistent particle size distribution of white fused aluminum oxide, facilitating an even finish and maintaining structural integrity.
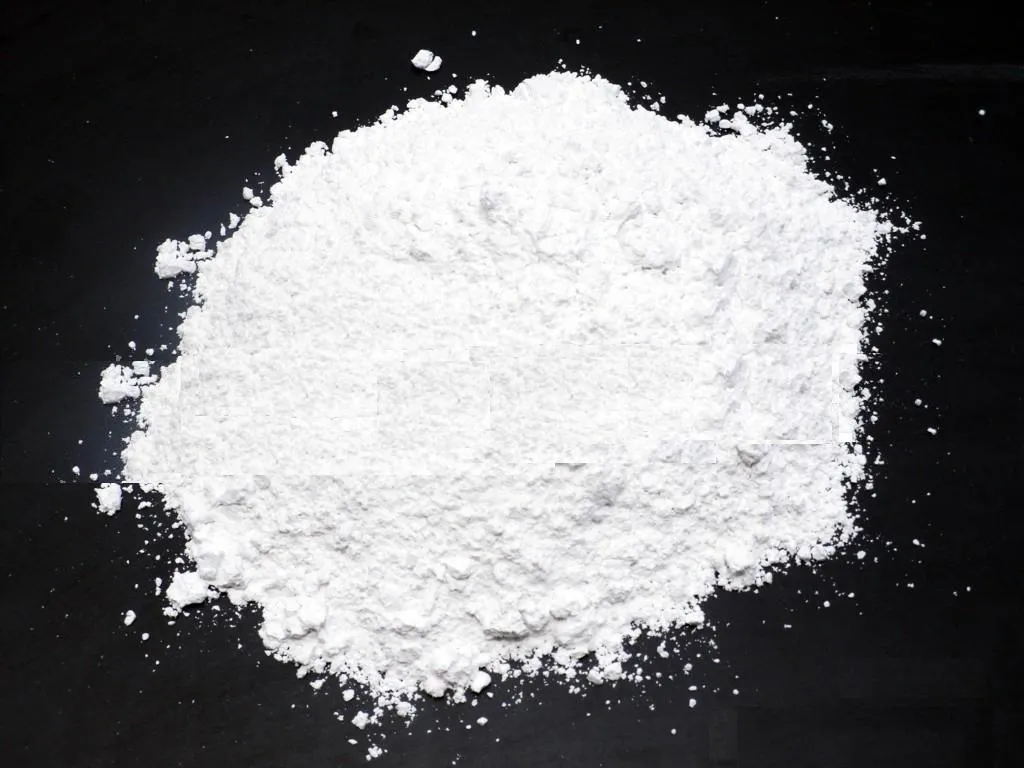
When evaluating the authoritativeness of white fused aluminum oxide, its implementation in high-temperature applications cannot be overstated. Refractory experts leverage its excellent thermal conductivity and high melting point, using it in products that endure severe thermal stress, such as kiln linings and high-temperature furnace linings. This material’s stability under extreme temperatures, coupled with its resistance to corrosion, underscores its effectiveness and reliability in sustaining operational integrity.
white fused aluminium oxide
Trustworthiness in material performance is essential, and white fused aluminum oxide delivers by maintaining a steadfast dependability across multiple sectors. In sandblasting applications, for instance, it not only removes surface impurities with precision but does so without compromising surface profiles needed for subsequent coatings. Its recyclability in abrasive blasting further reinforces its economic and environmental appeal, offering industries a sustainable solution that does not sacrifice quality or performance.
From an experiential standpoint, professionals utilizing white fused aluminum oxide consistently report that its efficiency in cutting down operational time and enhancing output quality justifies its initial cost. This material enhances productivity by reducing the need for frequent material changes or maintenance, directly translating into cost savings and improved workflow dynamics. Many industry veterans have come to rely on its predictable and high-performing characteristics as a benchmark for superior abrasive processes.
In summary, white fused aluminum oxide's unique blend of hardness, purity, and thermal stability sets it apart as an authoritative choice in a multitude of demanding industrial applications. Its expert-endorsed use extends across abrasive machining, surface treatments, and refractories, reaffirming its status as a trusted material. With a commitment to performance and quality, white fused aluminum oxide stands as a testament to engineering excellence, ensuring that industries continue to push the boundaries of what is possible.