Silicon powder of 325 mesh size plays a pivotal role in various industrial applications, leveraging its fine granularity and unique properties. When discussing the intricate realm of silicon powders, a comprehensive understanding of its capabilities, benefits, and applications not only highlights its professional merits but also affirms the trust in its utility. Below, we delve into this fine material, bringing to light cutting-edge insights and tangible expertise.
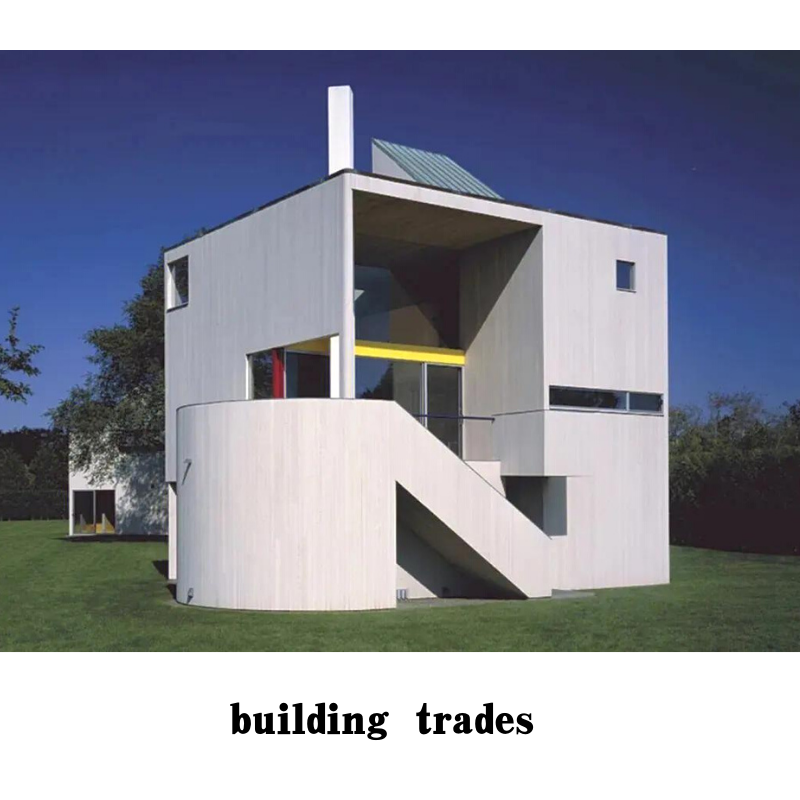
The utility of silicon powder primarily revolves around its size and fineness, which is measured using a mesh scale. At 325 mesh, the powder is characterized by its ability to pass through a screen with 325 openings per inch, underscoring its extremely fine nature. This fineness is what equips the powder with a wide range of applications, particularly in industries such as metallurgy, electronics, and thrust areas like advanced ceramics and refractories.
One of the critical experiences shared by industry professionals is the powder's role in metallurgical processes. Silicon powder is utilized to enhance the mechanical properties of alloys, acting as a deoxidizing agent where its reactivity is precisely what engineers rely on to prevent molten metals from oxidizing. Experienced metallurgists often highlight the indispensable nature of silicon powder in producing ferrosilicon and in the precision crafting of aluminum-silicon alloys, crucial to automotive and aerospace industries.
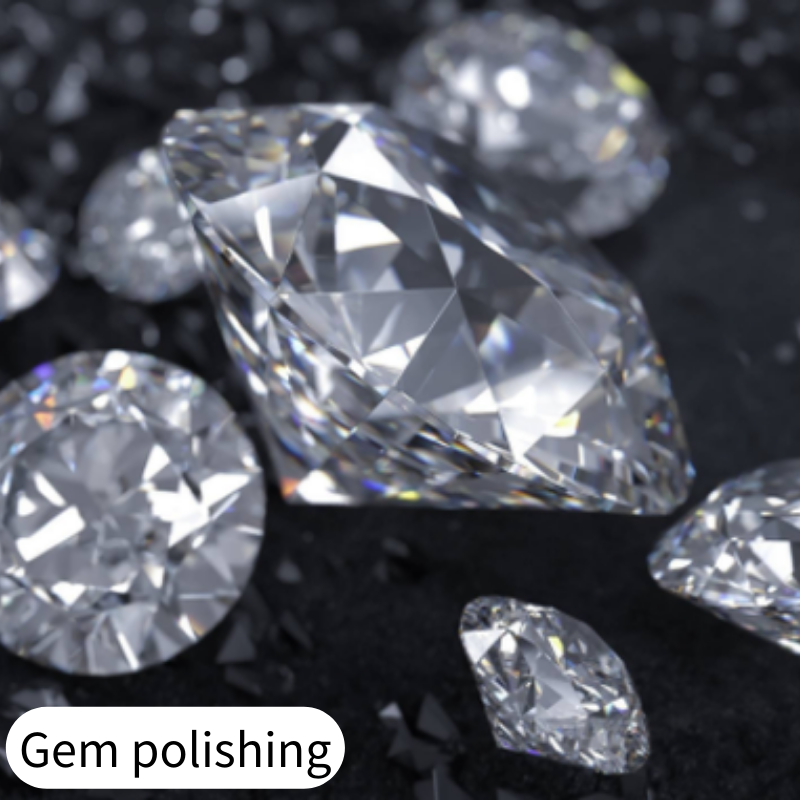
In the competitive sphere of electronics, the expertise around silicon powder of 325 mesh size is evident in semiconductor fabrication. Its fine granularity allows for enhanced control and purity in silicon wafers production, crucial for producing advanced integrated circuits (ICs). Professionals in the semiconductor field acknowledge the powder's purity and consistency as fundamental to achieving high-performance chips, essential to the functioning of modern digital devices.
Another domain where silicon powder proves its superiority is in the production of advanced ceramics and refractories. Its fine nature allows it to be an excellent component in ceramic production, aiding in achieving desired strength and thermal resistance. Authoritative voices from materials science emphasize its role in improving thermal shock resistance and maintainability, making it a preferred choice for applications that demand high durability and thermal stability.
silicon powder 325 mesh size
Trust in the efficacy of silicon powder at 325 mesh size is reinforced by stringent quality standards followed in its production. Manufacturers often provide detailed certifications reflecting particle size distribution, purity levels, and performance metrics, ensuring that industries have reliable data to base their usage on. This level of transparency and adherence to regulations provides assurance to engineers and project managers who depend on these metrics for project planning and execution.
Moreover, the environmental and sustainable aspects of silicon powder production cannot be overlooked. Manufacturers are increasingly adopting eco-friendly processing techniques to ensure minimal environmental impact, a move that aligns with global sustainability goals. The commitment to sustainable practices not only strengthens trust but also adds to the authoritative position of suppliers committed to reducing carbon footprints and promoting green manufacturing.
For end-users and industry experts alike, staying informed about the latest research and technological advancements connected to silicon powder is crucial. Engaging with academic publications, participating in industry conferences, and collaborating with research institutions are recommended paths for maintaining expertise. By constantly updating their knowledge, professionals can better harness the capabilities of silicon powder, innovating and improving upon existing applications.
In summary, silicon powder of 325 mesh size is more than just a component; it's a cornerstone material that supports multiple high-tech and industrial applications. Its centrality to fields such as metallurgy, electronics, and ceramics underscores its ability to meet demanding performance standards. Coupled with a commitment to sustainability and backed by authoritative research and quality control, silicon powder continues to be a trusted and valued resource, playing a critical role in driving forward technological and industrial advancements.