The production of silica fume has become an industry cornerstone, renowned for its role in enhancing concrete performance. As a vital byproduct of silicon and ferrosilicon alloy production, silica fume represents more than just an industrial offshoot—it symbolizes a driving force for sustainability and innovation in the construction sector. This article aims to delve into the intricacies of silica fume production through the lens of real-world experience, expertise, and authoritative insight.
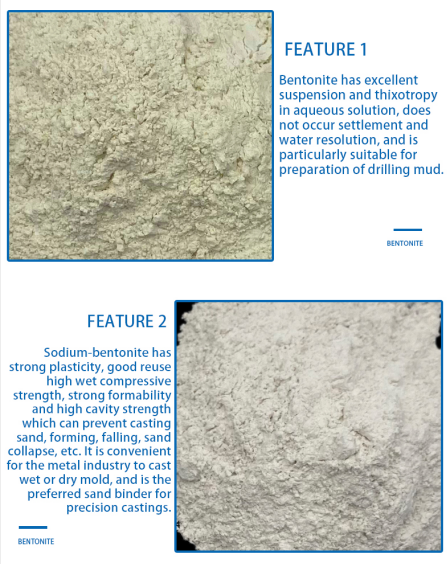
Silica fume production traces its origins to the 1950s, when its application potential was first recognized amid the voluminous exhaust gases of silicon metal smelting. The fume is collected through an advanced filtering process where silicon dioxide (SiO2) particles are extracted. These ultrafine particles, boasting a spherical shape and high pozzolanic activity, emerge with diameters less than 1 micron. This unprecedented fineness and reactivity bestow silica fume with its characteristic virtues, redefining its use in concrete reinforcement.
The modern process of harvesting silica fume involves cutting-edge technologies utilized in submerged electric arc furnaces. Here, the controlled reaction of quartz and carbon materials such as coal and coke yields silicon metal or ferrosilicon alloys. Throughout this process, silica fume can be collected through high-efficiency baghouse filters, capturing up to 90% of the resulting dust while absorbing the remaining particle emissions. This operational methodology consolidates the industry's commitment to environmental stewardship.
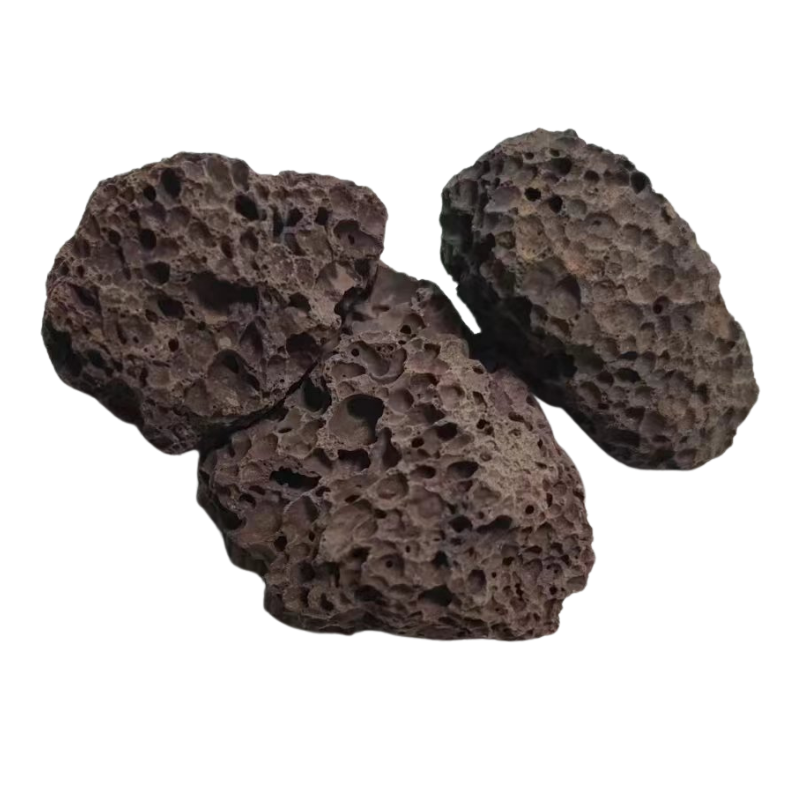
Expertise in silica fume production mandates a deep understanding of its transformational effects on concrete. When integrated into concrete compositions, silica fume lowers permeability and enhances compressive strength, yielding a denser structure. The secret lies in the physical and chemical interactions; the ultrafine particles fill voids and react with calcium hydroxide to form calcium silicate hydrate, the binding powerhouse of concrete’s strength. Construction professionals witness firsthand the reduced porosity and augmented durability—tangible evidence of silica fume's prowess.
silica fume production
Testaments to its authoritative influence permeate globally renowned projects where downtime is not an option. High-rise buildings, bridges, and tunnels constructed with silica fume-enriched concrete enjoy prolonged lifespans under arduous conditions. Dubai’s Burj Khalifa, the Channel Tunnel, and numerous U.S. freeway overpasses have incorporated this material, evidencing an unparalleled trust within the civil engineering community.
Transparency and trustworthiness in silica fume production are paramount. Leading manufacturers adhere rigorously to quality standards such as the ASTM C1240 and EN 13263, ensuring consistent particle size distribution and purity. By ensuring these criteria, producers not only affirm their commitment to quality but also reinforce the reliability of silica fume as a premium concrete additive. Moreover, the transparency in production processes builds confidence among stakeholders, from engineers and architects to end-users.
The sustainability aspect cannot be overstated. By utilizing a byproduct that otherwise might contribute to industrial waste, the silica fume industry exemplifies circular economy principles. The reduced need for primary raw material mining leads to a significant minimization of environmental impact—a key consideration for stakeholders attuned to eco-friendly development strategies.
In conclusion, the production of silica fume stands as a testament to industrial expertise, delivering cutting-edge solutions to the construction industry's most pressing challenges. This ultra-fine material embodies the synthesis of experience and innovation, fortifying infrastructures that underpin modern society. As demands grow for sustainable construction practices, silica fume's pivotal role is poised to expand, cementing its reputation as an exemplary model of industry-proven reliability and environmental responsibility.