Silica fume, also known as microsilica, has emerged as a transformative material in the construction industry, particularly when used in concrete mixes. This ultrafine powder, a byproduct of silicon and ferrosilicon alloy production, is lauded for its ability to enhance the properties of concrete, making it an invaluable component in high-performance construction projects.
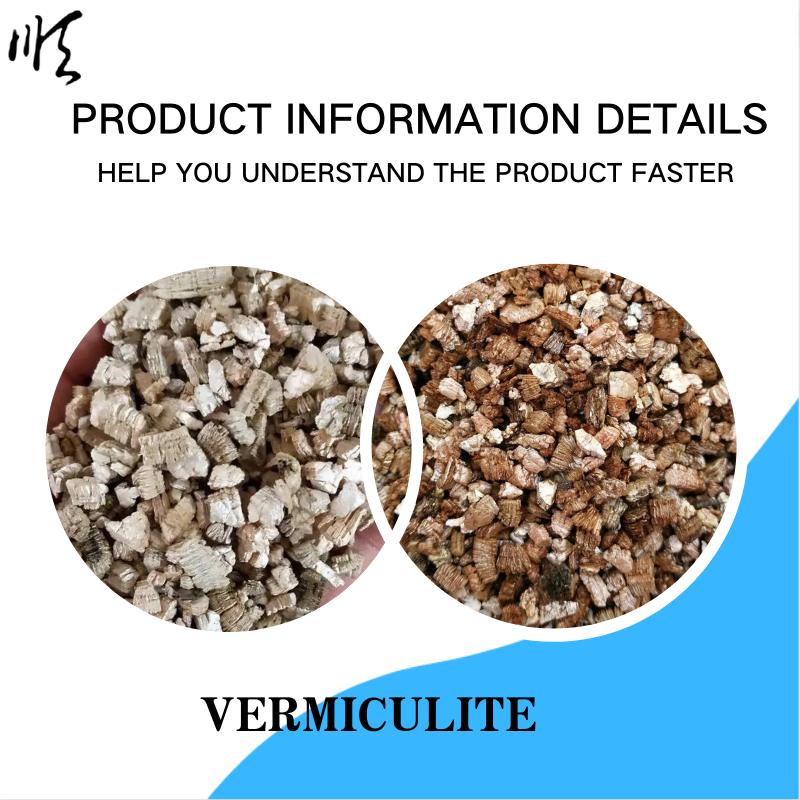
Builders and engineers have consistently praised silica fume for its ability to significantly improve the strength and durability of concrete. When silica fume is added to concrete, it acts as a pozzolanic material, reacting with the calcium hydroxide produced during cement hydration. This reaction results in the formation of additional calcium silicate hydrate (C-S-H), which is the primary substance responsible for concrete's strength. As a result, the presence of silica fume can increase the compressive strength of concrete by as much as 30%, making it an ideal choice for constructing high-rise buildings, bridges, and other load-bearing structures.
In addition to its strength-enhancing properties, silica fume also contributes substantially to the durability of concrete. Due to its fine particles, silica fume fills the microscopic voids in the concrete matrix, reducing permeability. This low permeability is crucial in preventing the ingress of harmful chemicals and moisture, which can lead to the deterioration of concrete over time. Structures built with silica fume-enhanced concrete exhibit superior resistance to chemical attacks, sulfate attacks, and chloride penetration, all of which are common issues in environments exposed to harsh weather conditions or deicing salts.
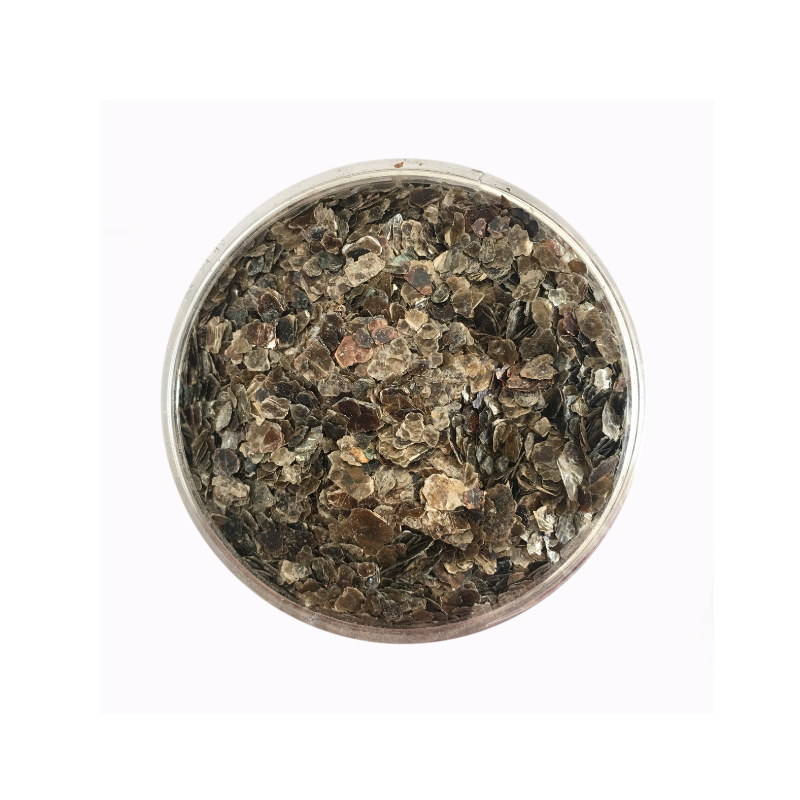
The benefits of using silica fume in concrete extend beyond mechanical improvements. Because of its dense packing, silica fume can help in reducing the occurrence of thermal cracking in large concrete pours. It minimizes the temperature differential between the core and the surface by lowering the hydration heat, thus reducing cracking risks that compromise structural integrity over time.
silica fume in concrete
Environmental sustainability is another critical factor where silica fume makes a positive impact. As a recycled industrial byproduct, its use in concrete diverts waste from landfills and reduces the carbon footprint associated with cement production. This aspect not only bolsters its acceptance as an environmentally responsible material choice but also aligns with the growing demand for sustainable construction practices.
Experts recommend careful proportioning and quality control when incorporating silica fume in a concrete mix. Its high surface area and density require precise calibration to avoid issues such as reduced workability. Builders often employ superplasticizers in conjunction with silica fume to maintain fluidity and ensure a uniform mix without segregation.
In recent years, the application of silica fume has seen innovative advancements beyond traditional concrete. Research is ongoing into its use in ultra-high-performance concrete (UHPC) and self-healing concrete technologies. UHPC, with its remarkable mechanical properties, owes part of its superior performance to silica fume. Meanwhile, in the realm of self-healing concrete, silica fume contributes to the formation of more C-S-H, which is instrumental in sealing micro-cracks that develop over time.
Silica fume has thus firmly positioned itself as a vital component in modern engineering practices. Its contributions to the strength, durability, and sustainability of concrete ensure its continued importance. Construction professionals and engineers can rely on silica fume's proven track record and ongoing innovation to meet the demands of today's complex construction challenges while preparing for the future.