Fly ash and silica fume have become indispensable components in the concrete industry, especially when aiming to enhance the durability and sustainability of structures. These supplementary cementitious materials bring a plethora of benefits that align perfectly with modern construction demands. Leverage the unmatched properties of fly ash and silica fume for superior concrete products.

Fly ash, a byproduct of coal combustion in power plants, has gained recognition as an eco-friendly solution in concrete production. Incorporating fly ash into concrete not only diverts waste from landfills but also improves concrete performance. This material enhances the workability of the concrete mixture due to its spherical particle shape, which acts like miniature ball bearings, reducing the water demand. In practice, this means less water is required for mixing, leading to higher strength and reduced permeability. Concrete structures become more resilient to environmental assaults like freeze-thaw cycles and sulfate attacks, thus extending their lifespan significantly.
On the other hand, silica fume, a byproduct of silicon and ferrosilicon alloy production, is revered for its ultra-fine particles. When added to concrete, silica fume dramatically increases strength and reduces permeability, primarily due to its pozzolanic properties. It reacts with calcium hydroxide in the mix to form additional calcium silicate hydrate, which is the compound that lends concrete its strength. Structures like high-rise buildings and large bridges, which demand robust performance, benefit greatly from these enhancements. The reduction in permeability is particularly crucial, as it provides formidable resistance against chloride ions, a common perpetrator of rebar corrosion.
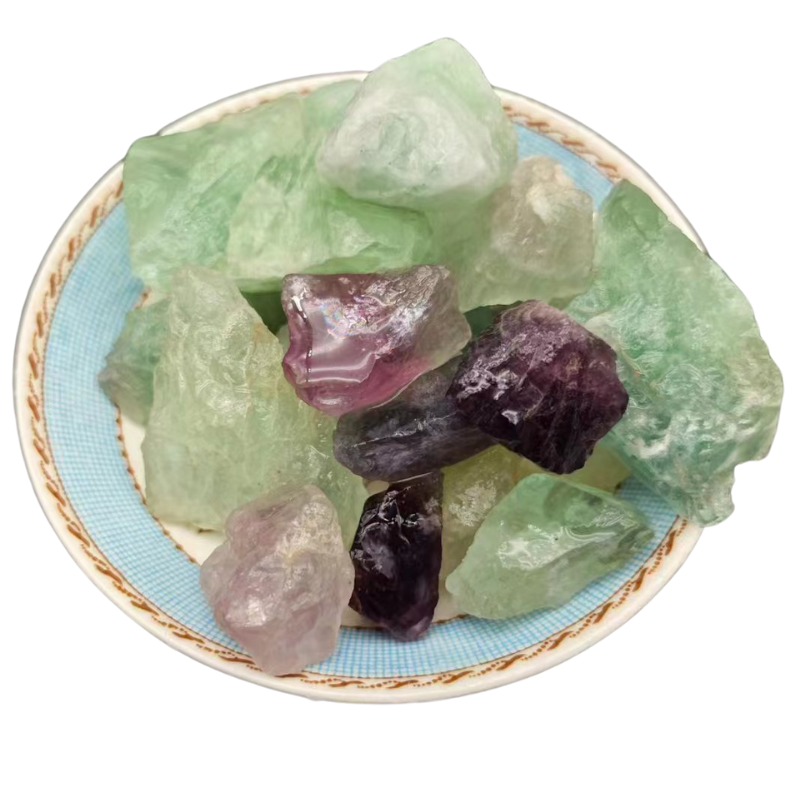
Combining fly ash and silica fume can take concrete's capabilities to new heights. Fly ash provides increased workability and contributes to long-term strength gain, while silica fume delivers immediate strength and impermeability. This synergy is especially beneficial in different sectors, from residential to industrial constructions, ensuring that the infrastructures not only meet but exceed engineering benchmarks for sustainability and longevity. By mitigating the thermal cracking potential, this combination is also suited for massive concrete pours where temperature control is critical.
fly ash and silica fume in concrete
For the construction industry, using these materials is not just about performance; it's also about cost efficiency and sustainability. Fly ash and silica fume reduce the Portland cement content necessary in concrete mixtures. Portland cement production is a significant contributor to CO2 emissions, thus utilizing fly ash and silica fume can considerably cut down the carbon footprint of construction projects.
However, the utilization of these materials requires expertise to manage potential challenges. Fly ash varying from different sources demands precise quality checks to ensure consistent performance. Silica fume's significant fineness may demand optimized mix design to avoid quick setting times or shrinkage issues. Partnering with reputable suppliers who understand and manage these nuances is crucial.
Concrete producers and construction companies should opt for documented and trial-tested methods when using fly ash and silica fume. This not only ensures compliance with standards like ASTM C618 and ASTM C1240 but also guarantees superior quality control. By doing so, companies enhance their reputation for quality and sustainability, meeting client expectations in the most demanding projects.
In a world where ecological consideration is no longer optional, integrating fly ash and silica fume into concrete production is a testament to forward-thinking and responsible stewardship. It underscores a commitment to excellence and innovation in creating infrastructures that stand the test of time, environmental exigencies, and sustainability benchmarks.