Custom hollow glass beads, an innovative and versatile material, have found their niche in various industries due to their unique properties and endless potential for customization. These beads, characterized by their hollow structure and glass composition, are manufactured in specialized factories that cater to the specific needs of clients.
The production process of custom hollow glass beads begins with the selection of high-quality raw materials, primarily silica sand, soda ash, and limestone. These ingredients are carefully mixed and heated to extreme temperatures, transforming them into molten glass. The molten glass is then blown or extruded to create tiny, hollow spheres. The size, shape, and color of these beads can be tailored according to customer requirements, making them ideal for diverse applications.
One significant advantage of custom hollow glass beads is their lightweight nature, which reduces overall weight in products they are incorporated into, such as coatings, plastics, and composite materials. This property is particularly advantageous in automotive and aerospace industries where weight reduction translates into fuel efficiency and cost savings.
In the field of cosmetics, custom hollow glass beads offer opacity, shimmer, and texture modification, allowing for unique product formulations. They can be customized to achieve different levels of transparency, providing a range of visual effects in makeup and skincare products They can be customized to achieve different levels of transparency, providing a range of visual effects in makeup and skincare products
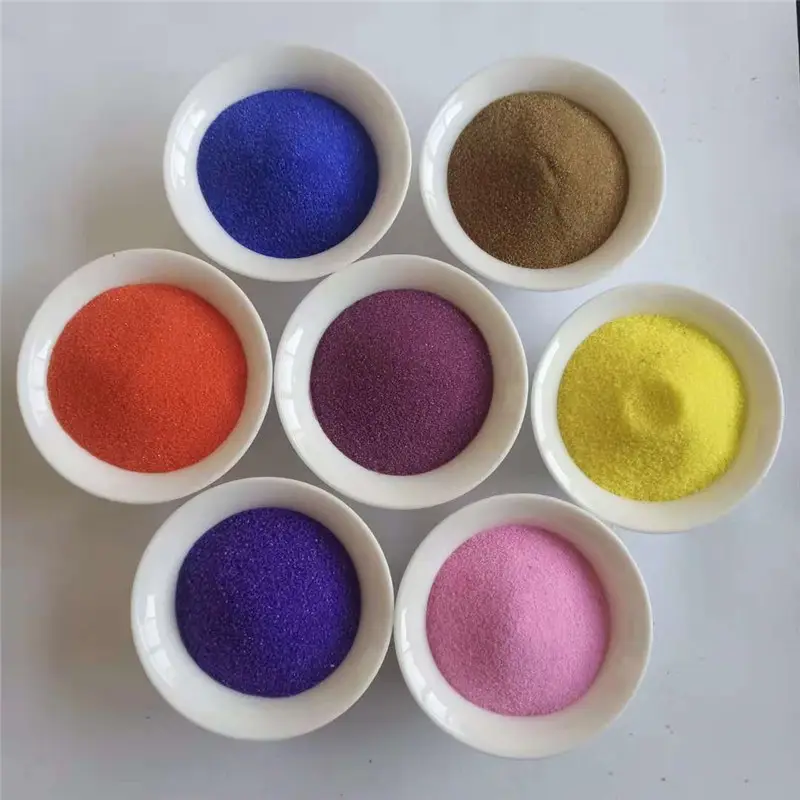
They can be customized to achieve different levels of transparency, providing a range of visual effects in makeup and skincare products They can be customized to achieve different levels of transparency, providing a range of visual effects in makeup and skincare products
custom hollow glass beads factories.
Moreover, these beads find use in the construction industry as fillers or additives in concrete, asphalt, and paint. Their hollow structure imparts improved insulation properties and reduced density, enhancing the performance of building materials.
Custom hollow glass bead factories often employ cutting-edge technology and skilled technicians to ensure precision and consistency in production. Quality control measures are stringent, ensuring beads meet the highest standards for durability, uniformity, and customization. These factories also prioritize sustainability, recycling waste materials and adopting eco-friendly manufacturing practices.
In conclusion, custom hollow glass bead factories play a pivotal role in catering to the dynamic demands of various industries. With their ability to produce beads with bespoke characteristics, these factories contribute significantly to innovation and progress across sectors. As technology advances and new applications emerge, the significance of custom hollow glass beads is likely to grow, solidifying their position as a valuable and adaptable material in modern manufacturing.