The Role of OEM Ceramic Sites in Plant Manufacturing
In the realm of plant manufacturing, Original Equipment Manufacturer (OEM) ceramic sites play a crucial role in ensuring that products meet high-quality standards while maintaining cost-effectiveness. These specialized facilities are dedicated to producing ceramic components and parts that are later integrated into various plants and machinery. By focusing on niche production, OEM ceramic sites contribute significantly to the efficiency and reliability of the final products.
Ceramic materials offer several advantages over other substances commonly used in plant manufacturing. They are durable, resistant to wear and tear, and can withstand extreme temperatures and harsh chemicals. This makes them ideal for applications such as filtration systems, heat exchangers, and catalytic converters. Moreover, ceramics are non-reactive, ensuring that they do not contaminate or alter the composition of materials processed in plants.
The importance of OEM ceramic sites lies in their ability to provide customized solutions tailored to specific industrial needs. These sites possess advanced technology and expertise to manufacture complex shapes and sizes of ceramic components with precision. They also adhere to strict quality control measures to ensure that each part meets the exact specifications required by the plant manufacturer. This level of customization is often impossible for larger, more generalized manufacturing facilities to achieve This level of customization is often impossible for larger, more generalized manufacturing facilities to achieve
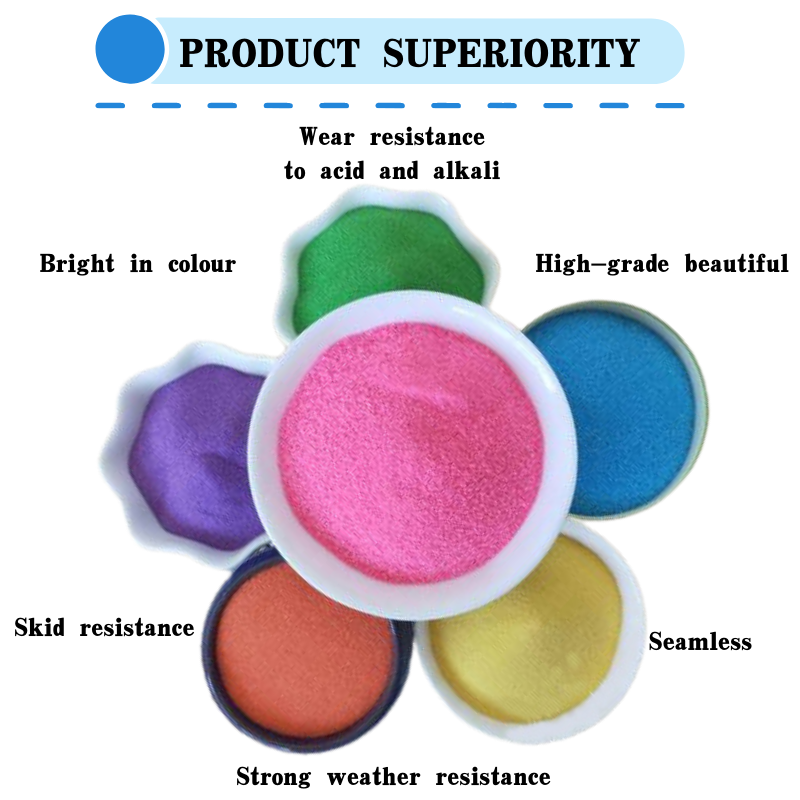
This level of customization is often impossible for larger, more generalized manufacturing facilities to achieve This level of customization is often impossible for larger, more generalized manufacturing facilities to achieve
oem ceramsite for plants manufacturer.
Furthermore, OEM ceramic sites typically operate with lean production methods, reducing waste and cutting costs associated with unnecessary processes. Their streamlined approach helps plant manufacturers reduce lead times and respond swiftly to changing market demands. The partnership between plant manufacturers and OEM ceramic sites thus becomes synergistic, with both entities benefiting from optimized production workflows.
Collaboration with OEM ceramic sites also allows plant manufacturers to focus on their core competencies. Instead of investing heavily in ceramic production capabilities, they can rely on these specialized providers to supply high-quality components. This division of labor enables plant manufacturers to innovate in other areas, such as improving system designs or enhancing automation features, without being bogged down by the intricacies of ceramic manufacturing.
In conclusion, the collaboration between plant manufacturers and OEM ceramic sites is a testament to the modern industrial trend toward specialization and outsourcing. As the demand for sophisticated plant equipment continues to rise, the partnership between these two sectors will undoubtedly continue to flourish, driving advancements in manufacturing and contributing to the overall progress of industrial processes.