Aluminium oxide, often referred to as alumina, is a popular abrasive material used in sandblasting processes across various industries. Its impressive qualities make it a top choice for achieving superior surface preparation and cleaning, especially when precision and efficiency are paramount. For those in the market for a dependable sandblasting medium, appreciating the distinctive properties of aluminium oxide can enhance understanding and decision-making.

One of the standout features of aluminium oxide is its hardness. Ranking at about 9 on the Mohs scale, similar to sapphires and rubies, it is robust enough to cut through various materials while being less susceptible to deformation. This hardness ensures the abrasive consistently delivers high performance, contributing to its long lifespan and reducing the need for frequent replacements. Users thus experience cost savings over time, a significant consideration for large-scale operations.
In addition to its hardness, aluminium oxide boasts a high melting point of over 2000 degrees Celsius, making it suitable for environments involving high temperatures. This thermal stability ensures that the abrasive maintains its integrity and does not break down under heat, a valuable trait for industries such as aerospace and automotive, where extreme conditions are the norm. The expertise needed to handle such jobs is enhanced by understanding how aluminium oxide can handle severe thermal cycles without losing effectiveness.
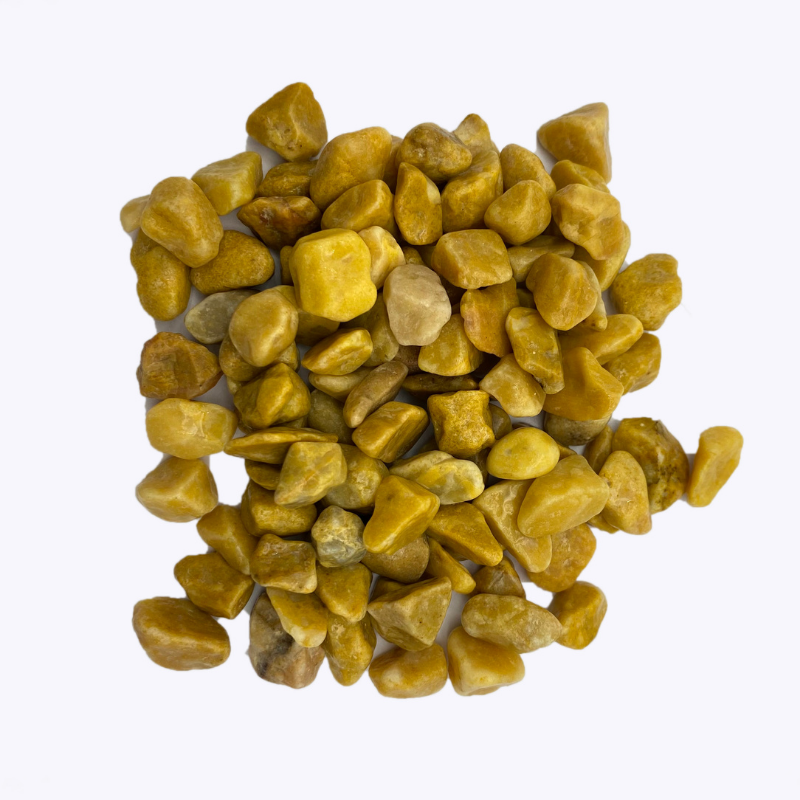
The grain shape of aluminium oxide is another factor that makes it ideal for precision work. Its angular particles make it effective in removing paint, rust, and other surface coatings without over-abrading the underlying layers. The consistency in particle size distribution enhances surface finish uniformity, which is crucial in industries where surface specifications are critical. Such reliability in surface finish improves trust between suppliers and customers who expect high standards of quality.
aluminium oxide for sandblasting
Environmentally, aluminium oxide is considered a preferable option as it is reusable, which minimizes waste generation. Its recyclability is enhanced by its resilience, allowing for multiple uses before disposal is necessary. Companies that prioritize sustainable practices find this feature particularly beneficial, aligning with modern eco-conscious values. Trustworthiness as a responsible business partner is bolstered when utilizing materials that contribute to sustainability.
Handling and storing aluminium oxide require certain precautions, highlighting the need for expertise. It should be kept in a dry, controlled environment to prevent moisture uptake, which can impact its performance. Additionally, safety measures must be adhered to, such as using protective gear to avoid inhalation of fine particles during application. This recognizes the importance of health and safety standards, which any authoritative company would insist upon.
Lastly, the global availability of aluminium oxide adds to its appeal. Sourced from bauxite and refined globally, it ensures supply chain reliability, a crucial factor in large enterprises or projects with tight schedules. Having predictable access to such material enhances operational planning and execution, providing a logistical advantage to firms leveraging this abrasive medium.
In conclusion,
aluminium oxide serves as a dynamic and versatile material in sandblasting applications. Its formidable properties of hardness, thermal stability, precise abrasiveness, environmental sustainability, and global availability make it a premium choice within the industry. Understanding its unique attributes fosters better product application and industry standards, enhancing both the credibility and performance of businesses utilizing it. By focusing on these aspects, decision-makers can confidently incorporate aluminium oxide into their operations, boosting both efficiency and trust in their processes.